Introduction: Before the hydraulic pipe bender works, it is necessary to set the working parameters of the hydraulic pipe bender. Otherwise, the normal work environment of the hydraulic pipe bender cannot be realized. The description of the white point is to set the parameter environment of the hydraulic pipe bender.
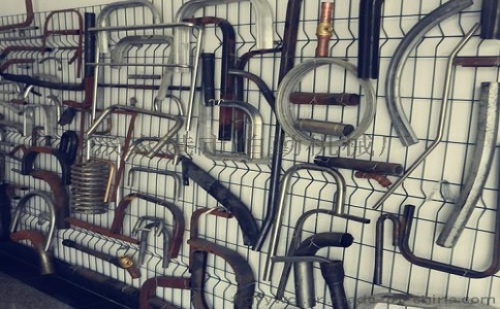
Note that the use of hydraulic tube bender design and pipe line pipe to avoid excessive arc, arbitrary curves, composite bends and greater than 180. The arc. Excessive arcs not only make the work tools bulky, but also are limited by the size of the hydraulic pipe bending machine; arbitrary curves and compound bends are very unreasonable, which greatly hampers mechanization and automatic production, making it difficult for operators to get rid of bulky manual labor. ; greater than 180. The arc makes the hydraulic pipe bender unable to remove the mold.
To ensure the normalized bending radius of the bending radius, try to achieve "one tube and one mold" and "multiple tube and one mold". For a pipe, no matter how many bends, the bending angle, there can only be one bend radius, because the hydraulic pipe bending machine does not replace the module during the bending process, which is "one tube and one mold." The "multi-tube-die" method means that the same diameter pipe should use the same bending radius as much as possible, that is, using the same set of modules to bend different shapes of the pipe shape, so that it is beneficial to reduce the number of modules.
Choosing the proper bending radius value of the bend radius of the pipe bender determines the resistance of the pipe during bending. In general, the large diameter of the pipe bend is small, and when wrinkling, wrinkles and slipping are likely to occur. The bending quality is difficult to guarantee. Therefore, the R value of the pipe bending die is generally 23 times the diameter of the pipe.
Set the moderate bending speed The main influence of the bending speed on the forming quality is: the speed is too fast, and it is easy to cause the flatness of the bent portion of the conduit, the roundness is not up to the requirement, resulting in the cracking and breaking of the conduit; the speed is too slow. It is easy to cause the wrinkling of the catheter and the pressure block to slip, and the tube with a large diameter tends to cause the sagging of the curved portion of the catheter. For a large number of tests on these two numerically controlled hydraulic pipe benders, it is advisable to determine the bending speed of the pipe as 20%–40% of the maximum bending speed of the machine.
Selecting a suitable mandrel and its position The mandrel of the hydraulic bender mainly acts as an inner wall supporting the bend radius of the catheter to prevent its deformation during the bending process. At present, if the domestic pipe is bent on a machine tool, if the mandrel is not used, the quality of the pipe cannot be guaranteed. There are many types of mandrels, such as cylindrical mandrels, universal single, double, triple, and four-ball headed mandrels, directional single, multi-ball headed mandrels, and the like. In addition, the location of the mandrel also has a certain influence on the bending of the catheter: In theory, its tangent line should be flush with the tangent line of the bending die, but after a lot of tests prove that the advance 1 ~ 2mm is better, then the quality of the elbow Ideal. Of course, if the advance amount is too large, the so-called “goose head†phenomenon will occur on the outer wall of the curved part. Here, we hope that everyone must pay attention to the parameter setting of each part of the manual pipe bender, which is directly related to whether the manual bending pipe can work normally. When setting the manual elbow, it must be set according to the instruction manual.
STF164 Series Alternator Suppliers
The insulation system is class 'H'.
All wound components are impregnated with materials and processes designed specifically to provide the high build
required for static windings and the high mechanical strength required for rotating components.
WINDINGS & ELECTRICAL PERFORMANCE
All generator stators are wound to 2/3 pitch. This eliminates triple (3rd,9th,15th) harmonics on the voltage waveform
and is found to be the optimum design for trouble-free supply of non-linear loads. The 2/3 pitch design avoids
excessive neutral currents sometimes seen with higher winding pitches, when in parallel with the mains. A fully
connected damper winding reduces oscillations during paralleling. This winding, with the 2/3 pitch and carefully
selected pole and tooth designs, ensures very low waveform distortion.
STF164 Series Copy Stamford Brushless Alternator
Copy Stamford Brushless Alternator,Three Phase Brushless Alternator,15 Kva Generator 3 Phase,11 Kva Alternator
FUZHOU LANDTOP CO., LTD , https://www.landtopco.com