In recent years, with China's power, steel, cement, waste incineration and other industries by leaps and bounds, China's bag filter technology, equipment level and industry have been leaps and bounds, bag filter design significantly improved the level of performance has reached or close to foreign countries Similar products. Bag filter dust removal design of the largest single from the original 1000000 m3 / h increased to 2.5 million m3 / h, the export concentration from the original 50mg / m3 strictly below 10mg / m3, running resistance from the original 1200 ~ 1800Pa reduced to 800 ~ 1200Pa, the air leakage rate can be controlled at <2%, unit processing air volume, steel consumption decreased by 15%, the design cycle from the average of 60 days to 30 days. At present, the bag filter has formed a series of products, and its application has covered all industrial fields and has become the mainstream dust removal equipment for air pollution control in China, especially PM2.5 emission control.
The new idea of ​​innovation and development is that the mode of air pollution control in our country changes from single governance to coordinated control. China has made some achievements in the field of metallurgical sintering furnace, garbage incinerator, coal-fired boiler and other fields and has formed an increasingly mature technology route.
1, sintering machine head flue gas co-governance island technology
In order to meet the new emission standards, the electrostatic precipitator and wet desulfurization combination, and the synergistic control process of electrostatic precipitator, circulating fluidized bed desulfurization and baghouse are gradually introduced, especially the fluidized bed desulfurization and bag type Dust removal as the core of the LJS dry multi-pollutant collaborative island management technology route shows its comprehensive technological advantages, and access to a wide range of applications.
2, solid waste incineration flue gas synergistic treatment technology
"Incineration power generation" is the most effective way to reduce, detoxify and recycle garbage. After being subjected to the tide of "anti-burning" two years ago and the project tempering in recent years, this approach proves that this approach is in line with China's national conditions so that it will embark on a stage of rational development and gradually form and establish a dust-bag-based system to handle waste incineration Gas dry, semi-dry and dry + semi dry combination of collaborative control technology route.
3, coal-fired boiler flue gas synergistic treatment technology
(1) Low-temperature electrostatic precipitator as the core of low-emission co-treatment technology
Pre-SCR + FGC + LLT-ESP + WFGD + WESP + FGR, is the lowest emission of coal-fired boiler flue gas Collaborative governance of the luxury configuration.
The advantage of this combination is that it has a wide range of adaptability to boiler type, coal type and combustion conditions. With the terminal convergence control of wet electric power, the requirements of ultra-low emission of multiple pollutants can be stably met. The disadvantage is that once an investment is high and the energy consumption is large , Covers an area, high operating costs, large maintenance workload. Technical and economic comparisons should be made and prudent decisions should be taken.
Low-temperature electric dust removal and ultra-low emission synergistic treatment technology is applicable to new or ultra-low emission reconstruction projects of large units in coal-fired power plants. Up to now, more than 20 sets have been designed and used, of which 6 sets of 1000MW have been put into operation, of which half have been put into operation to achieve the most stringent (≤50mg / m3, ≤35mg / m3, ≤5mg / m3) of ultra-low emission requirements.
(2) The ultra-low emission synergistic treatment technology based on wet clean desulfurization in single tower and three districts
Synergistic treatment process: SCR + ESP + SJ-WFGD is a practical configuration for synergistic treatment of coal-fired boiler flue gas with ultra-low emission.
The three-zone layout of the wet clean desulfurization tower, desulfurization at the same time, effectively remove PM2.5, SO3 and secondary dust to prevent the formation of "gypsum rain" with synergistic control. Three district tower compact structure, small footprint, investment, low operating costs, do not increase the wastewater treatment facilities. The disadvantage is that when the upstream ESP dust removal efficiency is unstable, the export of dust concentration is high, will result in fouling desulfurization tower plug, seriously affect the desulfurization effect and normal operation, demister overload failure.
Three districts wet desulfurization tower ultra-low emission synergistic treatment technology in the desulfurization system to meet the synergistic removal of SO2, PM2.5 fine particles, gypsum slurry, SO3 aerosols, ammonia aerosols and heavy metals and other solid particles to achieve a variety of pollutants Low emissions. On the basis of a small test of a 2 × 65t / h coal-fired boiler in Shanghai, it has been popularized and applied to small and medium-sized units in several power plants.
(3) Ultra-low emission co-treatment technology with ultra-clean electric bag compound dust removal as the core
Synergistic combination of control: FG + FGC + ESP + BF + WFGD + FGR is the lowest emission of flue gas from coal-fired boiler. Innovative configuration of collaborative governance.
The basic idea of ​​this combination is to emphasize denitration, dedusting and desulphurization, which do their job independently of each other and do not depend on the end wet electrostatic precipitator. With the concept of correct, technologically advanced, reasonable configuration, stable operation of the characteristics of investment, less land, low energy consumption, easy maintenance, without increasing wastewater treatment facilities, comprehensive technical and economic performance, suitable for large and medium-sized coal-fired boiler unit Low emission co-governance project.
(4) Ultra-low emission and dry-dry synergistic treatment with circulating fluidized bed desulfurization and baghouse dust as the core
Circulating fluidized bed (CFB) boiler fuel cycle in the furnace several times, while taking the second with the wind, oxygen and oxygen combustion and desulfurization and other measures, flammable anthracite, lean coal, gangue, are energy-saving boilers, mostly Matching generators below 300MW, accounting for a substantial share of small and medium power plants and heating centers. China now has more than 3,000 CFB boilers, with a total installed capacity of 6,300MW. CFB boiler tail flue gas with high concentration of particulate matter, SO2 and NOx content is low, suitable for circulating fluidized bed desulfurization and bag dust as the core of the whole dry synergistic treatment technology.
Synergistic treatment process: LNB, SNCR + ESP + CFB + BF, is the ideal choice for low and medium-sized coal-fired boiler flue gas Emission coordination of the whole dry-type configuration.
The combination for the whole dry process, energy saving, material recycling. Available CFB boiler high-calcium ash (or dry carbide slag) for CFB desulfurization agent, the dust layer on the surface of the filter bag involved in collaborative control, received the dust back to the CFB desulfurization tower for multiple recycling. Suitable for small and medium-sized coal-fired boilers, especially in the western region. The key to the normal operation of the system is to stabilize the construction of beds and logistics control cycle, the operation and maintenance management has high requirements.
Synergistic control index: NOx emission less than 50mg / Nm3; desulfurization efficiency greater than 95%, SO2 emissions less than 35mg / Nm3; particulate emissions less than 20mg / Nm3, the lowest 5mg / Nm3, PM2.5 removal rate greater than 90% % ~ 90%, mercury emissions less than 1μg / Nm3.
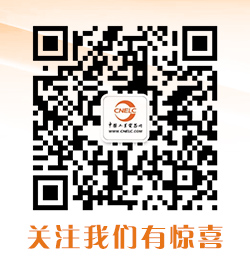
Automatic Paper Bag Machine is the ideal equipment to take the flat papers with original colors or printed well as raw materials to make into paper bags with square bottoms.Its technique process is about:the flat papers after printing are delivered into the driving parts for positioning through automatic paper feeder and press line with rolling press device and then make one-side glue, folding and positioning and sticking and conveying device will convey them into the bottom position and conduct press horizontal line,open bottom,make glue and press togther and finally output finished bag products.
Automatic Paper Bag Making Machine,Carry Paper Bag Making Machine,Paper Carry Bag Machine,Disposable Carry Paper Bag Making Machine
Wenzhou Xinlei Machinery Co. Ltd , https://www.xinleimachinery.com