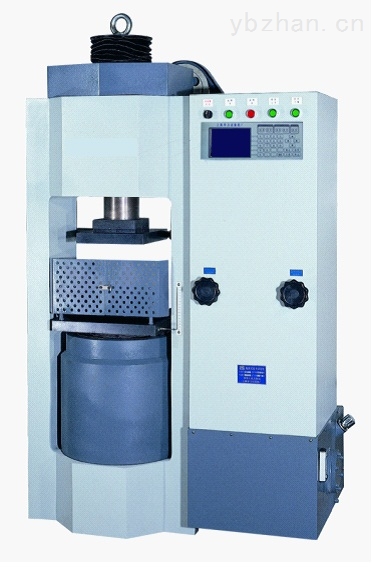
The press is a delicate structure versatility press. With a wide range of uses, high production efficiency and other characteristics, the press can be widely used in cutting, punching, blanking, bending, riveting and forming processes. The metal is processed into parts by applying a strong pressure on the metal blank to cause plastic deformation and breakage of the metal. When the mechanical press works, the motor drives the large pulley (usually doubled as the flywheel) through the V-belt, and the crank slider mechanism is driven by the gear pair and the clutch, so that the slider and the punch die linearly. After the forging work is completed, the mechanical press moves upwards and the clutch is automatically disengaged. At the same time, the robot above the crankshaft is connected so that the slider stops near the top dead center.
First, mechanical classification
1, screw press
The screw press uses a screw and a nut as a transmission mechanism, and a screw drive transforms the forward and reverse rotation of the flywheel into a forging machine that reciprocates up and down the slider. In operation, the motor causes the flywheel to spin up to save energy, while pushing the slider downwards through the screw and nut. When the slider contacts the workpiece, the flywheel is forced to decelerate to a complete stop, the stored rotational kinetic energy is converted into impact energy, and the slider is used to strike the workpiece and deform it. After the blow is over, the motor rotates the flywheel, causing the slider to rise and return to its original position. Screw press specifications are expressed using nominal work force.
2, crank press
The crank press is a relatively common cold stamping device and is used as a working platform for cold stamping dies. Its structure is simple and easy to use. According to the different structure of the bed, crank presses can be divided into open crank presses or closed crank presses ; according to the number of drive links can be divided into single-point press or multi-point press ; according to the number of sliders One or two can be divided into single-acting presses or double-acting presses .
3, friction press
Friction press is a universal pressure processing machine with a wide range of applications and can be used in various industries of pressure processing. In the machinery manufacturing industry, the application of friction presses is more extensive, and can be used to complete the work of forging, upsetting, bending, calibrating, sizing, etc. Some flashless forgings are also used in this press . carry out. Due to the omnipotence of presses in use, and the advantages of simple structure, installation, operation and auxiliary equipment, and low cost, they are used in stamping and forging workshops in industries such as machinery manufacturing, automobiles, tractors and aviation. Die forging workshops are widely used, and can also be stamping and refractory materials.
4, multi-station press
Multi-station presses are advanced press equipment, which is the integration of multiple presses. It is generally composed of a line head unit, a feeding mechanism, a press machine, and a line tail section. The fastest tempo can be up to 25 beats/minute or more to meet high-speed automated production. The thread end unit can be divided into the demolition unit, the magnetic belt and the cleaning, oiling equipment, etc.; the feeding mechanism is generally composed of feeding arms; the pressing machine can generally be divided into multiple sliders and single sliders, which can be based on different requirements. To make a selection, the end of the line generally consists of a conveyor belt.
Second, the mechanical structure
The press consists of four parts: an upright four-column hydraulic press; a combined control cabinet; an electric heating system and a heat preservation device; The above composition adopts an integrated design, which makes the model elegant and beautiful, and the compact structure is simple and reliable in operation and convenient in maintenance.
1. The pressurizing four-column hydraulic press should have reliable structural rigidity and anti-deformation ability, the position of the hydraulic station, the connecting device for lifting the mold by pressing, the hydraulic station and the removable dust cover. The workpiece can be out of length (3000). Technical parameters are as follows: Nominal pressure 190T; Effective table area 3000 × 750 mm2; Pressurizing movement speed 75 ~ 100 mm / s; Maximum opening and closing distance 550 mm (without heating plate); Holding time 8h (workpiece 130 °C ); press base height 0.5 ~ 0.55m; pressure row and base flatness 0.2 mm; press row base press average gap ≤ 0.25 mm (not less than 10 points).
2. Heating system The heating system consists of a steel heating plate, a heating pipe, and an insulation layer. Heating can be divided into two upper and lower plates, with each press of the base there is fixedly connected exclusion, and easy disassembly, the heating plate 45 # steel treated with high-tone Gong made. An electric heating tube and a thermocouple are placed in the heating plate. The thermocouple is fast and reliable to install and easy to disassemble. Heating plate technical parameters: plane size 3050×650 mm2; flatness 0.2 mm; measuring point arrangement: 3 points on the upper plate; 6 points on the lower plate. The outer shell material of the heating tube is stainless steel and the working voltage is 220V. Unilateral outgoing line, the number of multiples of 3. Electric heating tube replacement is convenient and reliable. There is a protective device at the connection. The insulation layer is arranged between the heating plate and the base (or pressure row), and the heating plate is provided with a material with good heat insulation performance. The plane size is equivalent to the heating plate, and the thickness is not less than 20 mm.
3. Control cabinet cabinet press operation and temperature combination cabinet. Meters and switches above the cabinet panel; power switches, indicator lights, voltmeters, ammeters; press buttons and indicator lights; pressure indicating instruments; heating switches and indicators; digital temperature controllers (accuracy ±1°C); Timer, over-temperature alarm; maximum operating temperature is 180°C; heating rate 1.7°C~2.5°C/min; temperature non-uniformity ±3°C, heating power of each phase power is balanced; temperature regulator corresponds to The real-time control of the temperature measurement area, when all reach the set value of ± 3 °C, the timer counts, after reaching the set time, the temperature control system can automatically warm or power off according to the process set value.
4, mold conveyor rack is an upper part of the rolling structure, one end connected with the press base (detachable), one end is placed on the ground above (adjustable height). Load capacity 3T; height roll on the surface flush with the next heating plate; plane size (2800 ~ 2900) × 750mm2 (available part); insulation board press on the press with the base around the base to reduce the mold heating process Loss of heat, made of aluminum (or stainless steel) and insulation. In order to facilitate placement can be divided into several pieces.
Third, the mechanical principle
The press is usually driven by the motor to drive the flywheel rim through the friction disk to rotate the flywheel, so this press can be called a friction press . China's largest friction press is 25 meganewtons. Larger presses use hydraulic systems to drive flywheels, also known as hydraulic screw presses . The largest specification is 125 meganewtons. Then came the electric press that directly driven the flywheel with a motor. It had a compact structure and a small number of transmission links. Due to frequent commutation, it required higher control electronics and required a special motor.
The rotary press has no fixed dead point. For larger die forgings, it can be formed by multiple blows, and can be used for singles, consecutive hits and inch moves. The impact force is related to the deformation of the workpiece. When the deformation is large, the impact force is small, and when the deformation is small (such as a cold strike), the impact force is large. In these respects it is similar to a forging hammer. But its slider speed is low (about 0.5 m/s, which is only 1/10 of the hammer), and the striking force will be closed by the frame, so the work is smooth and the vibration is much smaller than that of the forging hammer. Foundation. The press is equipped with a skid insurance mechanism that limits the maximum strike force to less than 2 times the nominal pressure to protect equipment safety.
The lower part of the press is equipped with a forging ejector. Screw presses have the functions of various forging machines such as die forging hammers and mechanical presses . They have strong versatility and can be used in die forging, blanking, deep drawing and other processes. In addition, screw presses , particularly friction presses, are simple in construction and easy to manufacture, so they are widely used. The disadvantages of screw presses are lower productivity and mechanical efficiency.
G80 Rigging Hardware,Hardware Rigging G80,Rigging Hardware for Chain,G80 Anchor Chain
Shandong Shenli Rigging Co.,LTD. , https://www.shenliriggingcn.com